
The swab and marking pen techniques are simple and rapid and are particularly useful for testing in the field or on curved, irregular, or porous surfaces where contact angles cannot be measured. ASTM D7541 describes cotton swab, marking pen, and drawdown techniques that simulate the application of a film. There are several simpler wetting/dewetting tests that can be used. However, contact angle measurements require specialized equipment and are not practical in the field. The standard method for doing this is the measurement of contact angles (see ASTM standards D7334 and D7490) where a low angle (5–30°) indicates adequate wettability and a high one (> 45°) signals possible problems such as contamination. There are tests to determine whether a surface is wettable. It is equally important to keep surfaces clean after these processes, especially when car bodies or parts are stored for even a day or two (such as over a weekend) before the painting process is completed. It is critical to ensure good cleaning and pretreatment of metals and power washing and solvent wiping of plastic parts. The defect usually is due to dirty or otherwise contaminated surfaces.

Unfortunately, when the coating is baked, any volatile contaminant such as a hydrocarbon or silicone oil is liable to be driven off in the oven This leaves nothing to analyze or such a miniscule amount that it takes expensive techniques like x-ray photoelectron spectroscopy (XPS or ESCA) or secondary ion mass spectrometry (SIMS) to identify it. However, contaminant identification is anything but easy and usually requires examination of individual craters by optical microscopy and analysis by techniques such as scanning electron microscopy, Fourier transform infrared microscopy (FTIR), and/or infrared microscopy. If the contaminant can be identified, then there is a good chance that its source also can be found. Rigorous inspections of paint shops have turned up sources such as poor substrate cleaning, oily overhead chains, smoking ovens, oil in the compressed air, and dirty paint booths, but often there is no obvious cause. Unfortunately, it is difficult to identify contaminants and their source. The majority of cases that I have encountered in auto plants have involved contaminants falling on the wet coating during or soon after application, but the other possible causes always must be considered. Craters vary in size and appearance, even from a given contaminant. Shallow craters often can be polished out, but deep ones require sanding and repainting. This produces a surface tension gradient that causes flow away from the low surface tension area, resulting in a circular low spot (see Figure 1 for an example). Craters are caused by low surface tension contamination that is on the substrate being painted, is in the paint, or falls on the paint. Nearly all coatings people are familiar with craters, but they may not know much about them.

These include craters, dewetting, telegraphing, picture framing (fat edges), and poor edge coverage. Many of the common day-to-day defects seen on car bodies are surface tension driven. Repairing of defects can lead to more problems, so the best strategy is to prevent them from occurring. All defects hurt appearance and some also can interfere with the corrosion or weathering protection aspects of the coatings.
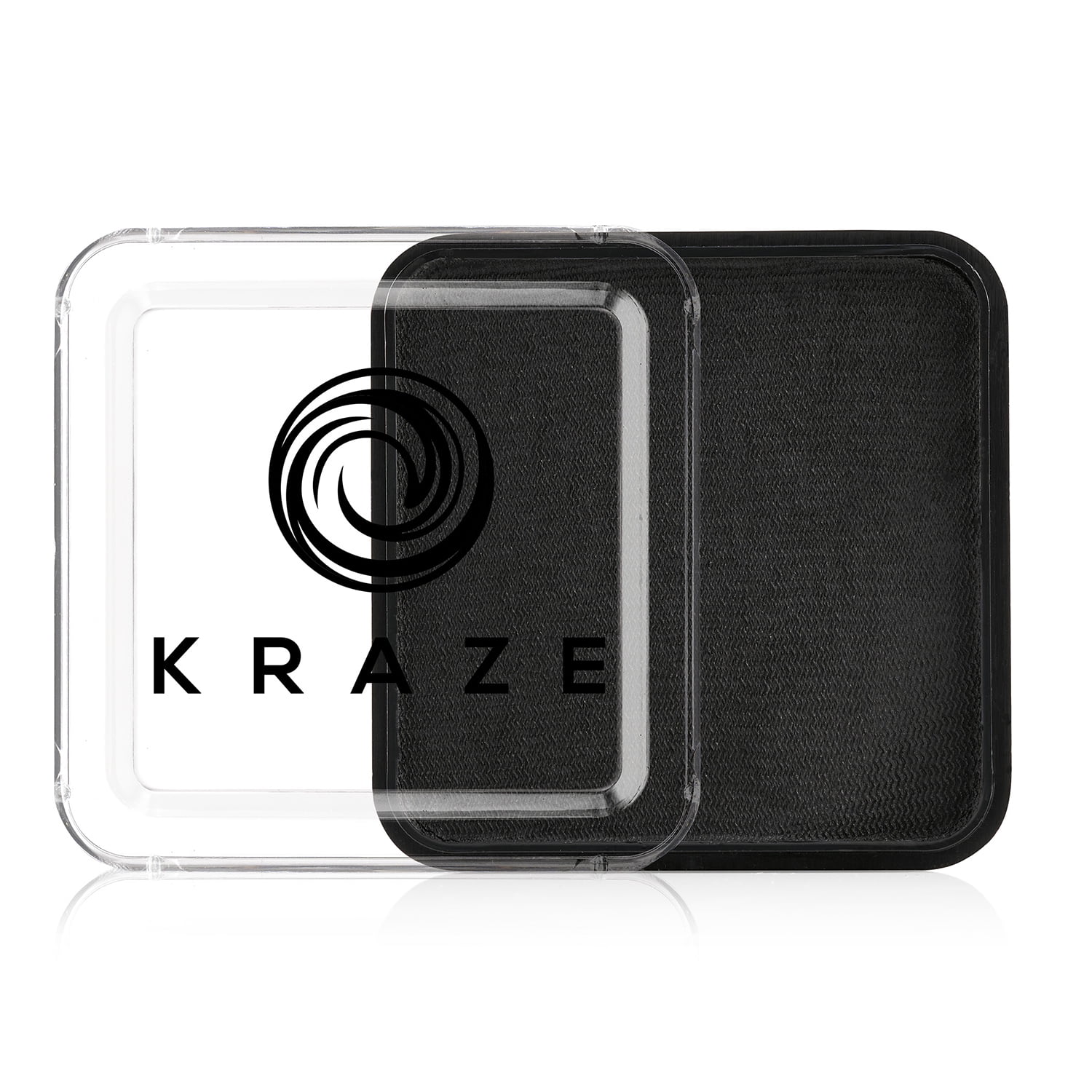
Craters undoubtedly are the most infamous and cause the greatest panic in the auto plant, but a number of other defects can occur. This article surveys some of the defects that automotive coatings experience when they are applied.

Spraying is the worst possible way to apply automotive coatings if minimization of surface defects is desired, but it is the only way to obtain the gloss, color effects, and outstanding appearance that car buyers demand.
